When working with machines or equipment we must be aware that their parts and components, which MPT Srl also deals with as a manufacturer of lathes and threads for flexible hoses, are subject to cyclic or variable loads which can cause failures due to wear. The production process, applied technology and materials are the key to preventing these problems. Here are some suggestions for subjecting materials to less stress.
The main causes of material wear are:
- Irregularities in the internal section of the material or discontinuities, even slight, which in the long run may generate problems
- Irregularities resulting from the machining processes undergone by the workpieces
- The geometric shape of the workpiece, which may influence the propagation speed of cracks.
- Environmental factors: wear due to temperature changes and corrosion.
It is precisely small cracks which should not be underestimated. If they form, they may cause the material to spoil prematurely.
The ends of these cracks are points at which tension builds up, and this tension increases whenever the object is subjected to a cyclic or variable load. Cyclic loads cause a state of internal tension which will widen the crack at its ends, since it is at these points where tension is most concentrated. As a result, the crack will be fated to grow more and more.
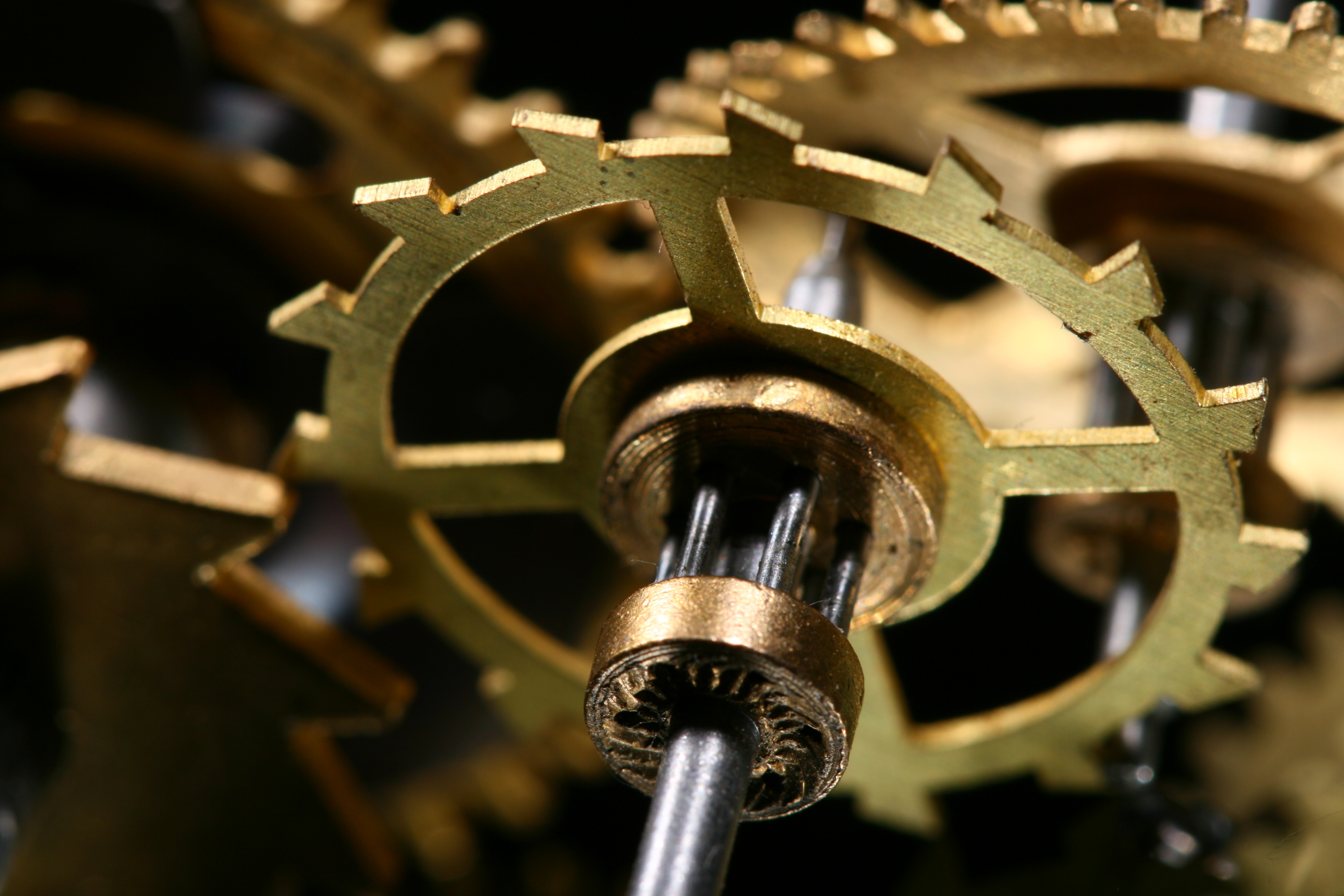
However, action can be taken to prevent such cracks from forming.
- First of all, it is necessary to thoroughly check the product realized, verifying the absence of variations in the sections of the component. This is the point at which stress is most concentrated, and this has a negative effect on the mechanical resistance of the material to natural movement caused by use.
- Evaluate the component geometry. This will affect the propagation speed of the crack. Beware of objects with changes in cross-section, holes or recessed corners. Such components are more likely to develop cracks and minor breaks. The geometry of the material also influences wear caused by stress: geometric discontinuities are points where stress accumulates more easily.
- Always pay close attention to the design, which must not exhibit structural irregularities, lines or sharp corners.
- Always improve and polish the surface of threads, lathes or components by polishing to remove small scratches or grooves which may be caused by cutting.
- Perform a surface hardening process by exposing the component to an atmosphere particularly rich in carbon or nitrogen at high temperatures. This will create a layer about 1 mm harder than the core material of the component.